
The trick of the trade – How do the PUR pads in the Sif Skybox concept work?
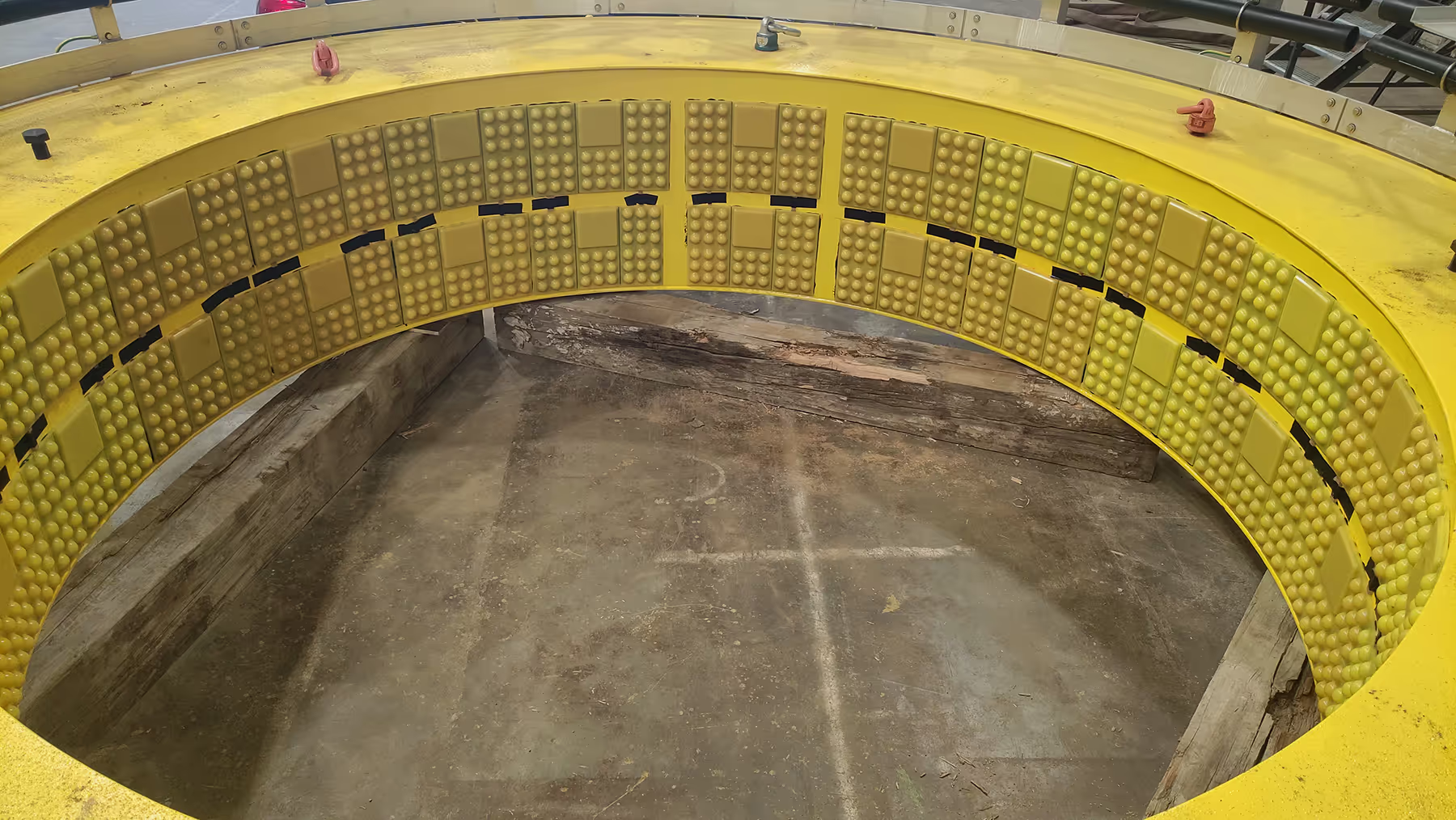
The perfect fit
Both parts are coated to withstand the offshore conditions, and it is vital to keep this coating intact over the installed lifetime of the monopile and skybox.
In addition to this, all fabricated parts are subject to fabrication tolerances, and the monopile and Skybox are no exception to this. Due to the nature of the conical slipjoint connection, these fabrication tolerances will have an influence on the settlement position of the Skybox over the monopile, both upon installation as well as over time. They also have an influence on the contact stress distribution in the slipjoint and in what form the loads coming from the skybox and acting onto the monopile, are distributed over a large as possible surface.
In the Skybox concept, both of these considerations are mitigated by the application of our specially engineered pads in the slipjoint connection between the monopile and the Skybox. The design team has tested multiple forms and found this solution to be the most suitable one.

Simultaneously soft & strong
For optimal distribution of the loads from the Skybox into the monopile, for optimal compensation of any fabrication tolerances, and for optimal coating protection, the pads would need to be rather soft and malleable. However this would come at a cost regarding load capacity and durability of the pads. To ensure that the pads will stay intact over the lifetime, and have sufficient load bearing capacity, they would need to be rather strong and stiff.
These are two contradicting requirements but after lots of research and testing, an optimum was found by choosing the right material type with properties that ensure the required stiffness, load bearing and durability capabilities, whilst the dedicated geometry of the tiles ensures the capability to compensate for tolerances and a constant and predictable (within a bandwidth) settlement position of the Skybox on the monopile.
The outcome of our development and testing is that the pads consist of a Polyurethane Rubber (PUR) material, with well designed material and geometrical properties.It was quite a challenge to get both of these in the correct working window.
Testing of the material was performed by OCAS N.V. and focussed on compression stiffness and strength, friction coefficients at different temperatures and load and humidity levels and included and aging test to represent the offshore conditions over time.
The resulting data was used by KCI to determine the correct properties for defining a material model that could be used in Ansys when designing a Skybox platform.

It comes down to the perfect shape
During our test activities with concrete and steel box scaled versions of the Skybox and at the OCAS material tests, we particularly found a strong influence of the so called shape factor of the PUR pads on the stiffness behaviour, after performing corresponding simulations in Ansys. When compressed, PUR needs to be able to expand (the so called Poisson ratio, which is around 0,45 for PUR). If the geometry does not allow for sufficient expansion then the pad behaves too stiff. This was the case at our first tests, where the individual pads were flat with a uniform thickness (100x100x20mm) and we could not find proper correlation between the real life tests and the simulations when it comes to settlement and stress distribution.
Upon these findings and proper further deliberation, we decided to change the geometry of the pads from a flat tile to a tile with domes on top. This geometry allows for expansion of the PUR material when subjected to a compressive load. And as an additional benefit, the stiffness of the pads is no longer linear, but increases progressively when compressed (since the domes get compressed more and more when loaded). This helps to initially overcome tolerances but also ensures sufficient load bearing capacity. This results in a narrower and more predictable bandwidth for the initial settlement position after installation of the Skybox on the monopile and in a better stress distribution.
It was decided to increase the original 100x100x20mm tiles to 200x200x30mm (where 20mm of the total thickness has a dome shape and 10mm is base material).
Then, taking it even one step further, 9 of the 200x200x30mmm tiles were combined into a mat with overall size 600x600x30mm. And for extra redundancy it was decided to have the centre tile of the 9 again as a flat tile so that in the unlikely scenario that the domes would fail for whatever reason, there is always one flat, slightly recessed, tile to bear the loads from the Skybox on the monopile.
This is now the standard PUR pad component which forms the key ingredient of the Skybox concept. The material type is selected and standardised, the geometry is defined and standardised, and every Skybox will have this PUR pad included as a standard component sitting in the slipjoint connection between the Skybox and the monopile. When monopile diameters, skybox sizes, or loads get bigger, the same PUR pad is intended to be used, only the number will be increased if required.
The standard PUR pad with all its properties and capabilities, and the route how we got to it is currently undergoing scrutinization by DNV with the aim to have a DNV component certificate in place by the end of 2025.
For designing a Skybox, the PUR pad properties are described and guaranteed by a design guide line document, containing all relevant parameters for the Ansys material model.
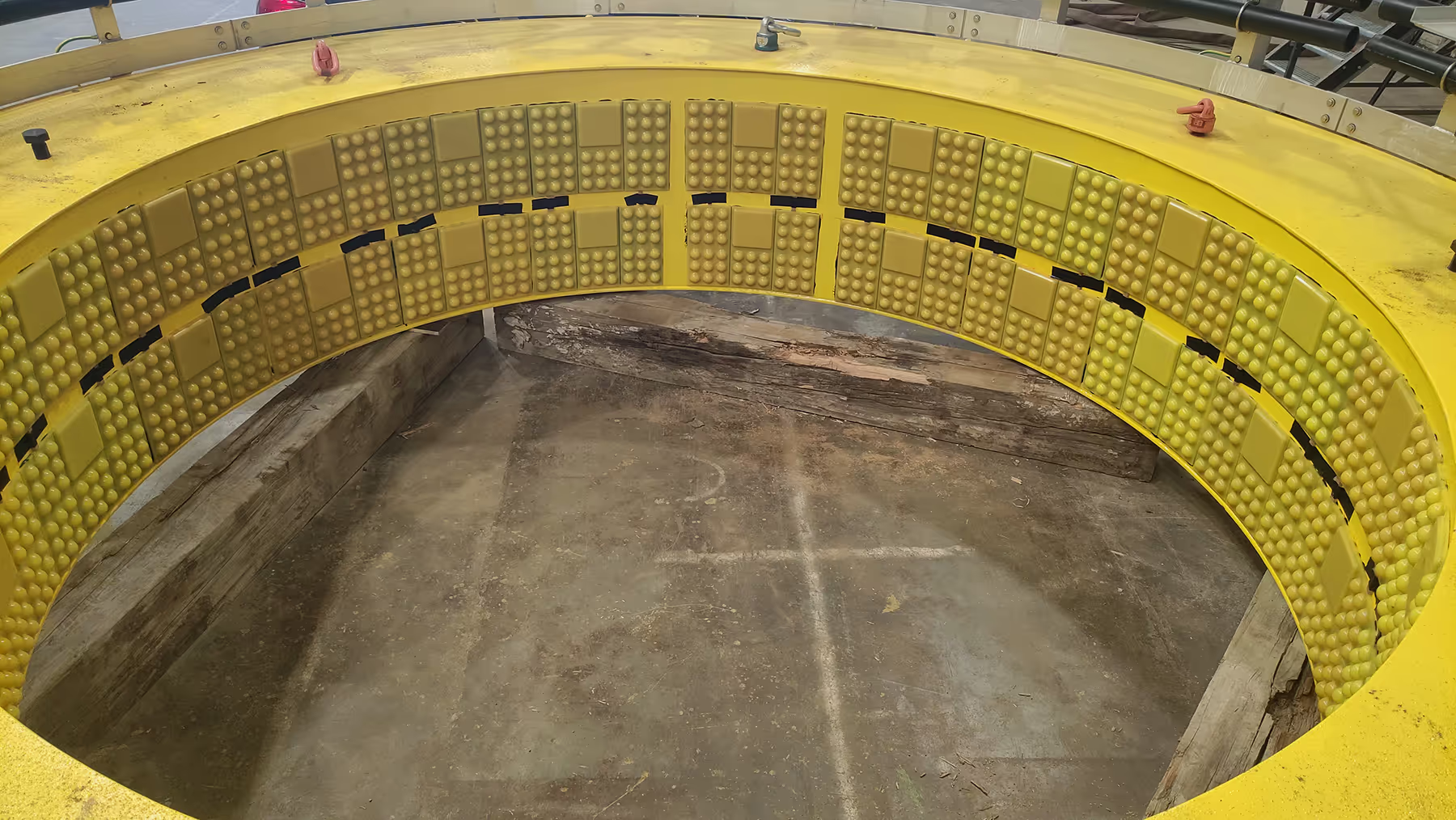

Stay on top, get skybox news
If you want, we will keep you updated on all intermediate milestone achievements of Skybox. By subscribing, you are kept informed of the progress we make in the development journey towards A-level certification and beyond.